Manufacturing in Vietnam: the “next China”?
Mechanical engineer and informal freelance member Brogan Miller, PE, recently visited 10 suppliers across 7 provinces in Vietnam to get a clearer picture of what should actually be built there. We’re excited to share his insights and high-level takeaways on Vietnam’s supply chain, labor force, and whether it’s truly poised to become the “next China.” If you’re in hardware manufacturing, this is definitely one to tune into.
In 2024, I asked the Stanford Product Design alumni group — a collection of every bachelor’s and master’s grad from the last 35 years — if they knew any Vietnamese 3D printing suppliers, and I only got one response. I was perplexed! How could Vietnam, lauded as a possible “next China,” be so poorly sourced by such an illustrious group?
So I went to Vietnam.
I’ve done this before. Fueled by naïve start-up energy, I quoted and visited over 50 factories across 11 cities in China, Taiwan, and Japan. I’m a New Product Introduction (NPI) versatilist. I don’t have 30 years of supply chain and ops experience — but I’ve shipped products with suppliers I sourced, brought up a low-volume ceramics factory in San Francisco, and denied bribes offered by suppliers. This braggadocio is context. I’m sharing my observations, insights, and raw data, and if you’re going to use my conclusions to make decisions, you’d better know who the dude behind the words is.
I started in Hồ Chí Minh, then headed north to Vĩnh Phúc, Hà Nội, Bắc Ninh, Hải Dương, Hải Phòng, and Bắc Giang. I visited suppliers doing machining, stamping, injection molding, springs, 3D printing, circuit board assembly (SMT), and final assembly, test, and packout (FATP). And I had substantive conversations with 25 folks — ranging from sales associates to general managers.
I firmly believe manufacturing is often more difficult than design because it’s as much about the technical as it is about the people. It takes a unique skillset to navigate both at once.
The “how to move your supply chain in the age of tariffs” guides are helpful, but they often lack the cultural extrospection necessary for real strategic sourcing. Have you ever been handed an obviously falsified first article inspection? Or had a material mysteriously change between builds? Those aren’t technical challenges. They’re people challenges.
What follows isn’t a whitepaper. This isn’t a regurgitation of a company deck. It’s real-world context from walking a dozen factory floors in the humid Vietnamese spring and breaking bread with the people actually doing the work.
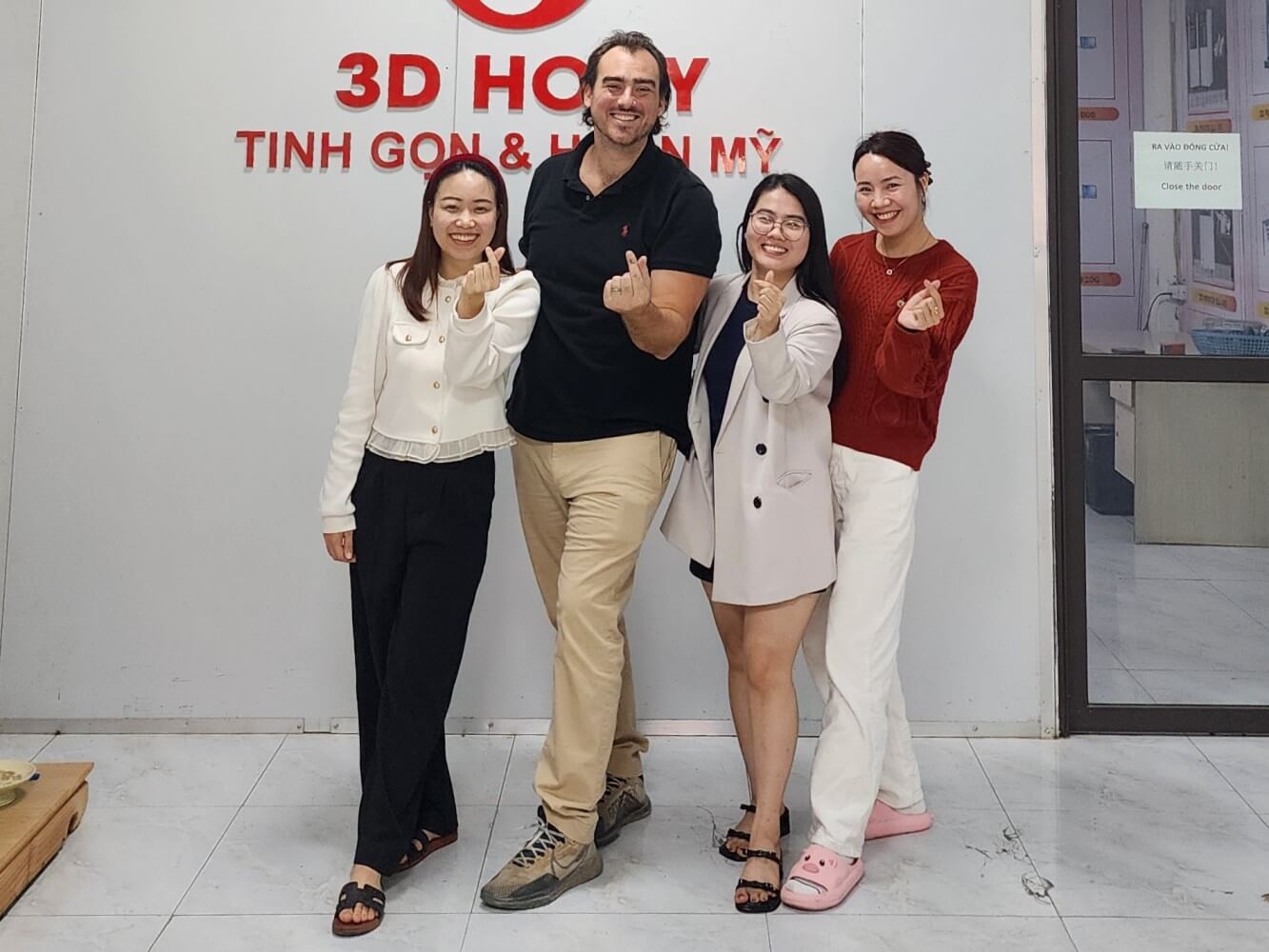
Guess which one is me
Supply Chain
If you’re considering manufacturing in Southeast Asia, it’s probably to avoid tariffs. But you can’t just build a part or assemble a product in a country and claim “Made in XYZ.” There are requirements — intentionally vague and hard to pin down — for achieving country of origin (COO). That’s a big reason I got my ass over there.
To be “Made in Vietnam” per Vietnamese regulation, you typically need to hit a regional value content (RVC) threshold of around 35% of your costed bill of materials (CBOM) and, depending on the product, you may need to have your SMT done in Vietnam. Importing countries may also have additional requirements for COO. Any off-the-books requirements are outside the scope of this article.
Seemingly straightforward — but tough in execution.
Every FATP operation I visited stuck close to the minimum RVC threshold — meaning they buy the remaining 65% of their CBOM outside Vietnam, usually from China because it’s cheaper. Likewise, Vietnamese part suppliers — plastic injection molders, metal fabricators, etc. — import their raw materials from China, Taiwan, Japan, or Korea because the domestic raw material infrastructure and maturity just isn’t there yet. Likewise, China heavily subsidizes their steel and aluminum industry, so expect to pay 30% more for Vietnamese metal.
SMT, depending on circuit board complexity, can require up to ~12 machines. If one goes down, the line stops—and you’re not making money. In China, you call your support engineer buddy, they show up in 30 minutes, and you’re back in action. In Vietnam, the support infrastructure is still being built, so there’s no savior a phone call away. They’re a flight away. This is especially true in Vietnamese-owned factories, which tend to prefer German or Japanese equipment.
This isn’t a knock on Vietnamese capability or potential; it’s just part of the development process, and Vietnam is firing up. Just one or two years ago, power outages were frequent. Every factory I visited had backup generators. But now, they rarely turn them on — especially the factories in industrial parks. One supplier credited this to recent Vietnamese government investment in domestic power infrastructure to reduce dependence on the Chinese grid.
Of the 10 factories I visited, half were founded in the last five years. Four are currently building new facilities, averaging around 16,000 square meters. One supplier even launched a new business unit and bought 1500 acres of land to help other companies establish new factories. Multiple senior level folks told me that the Vietnam of today reminds them of China in the late ’90s.
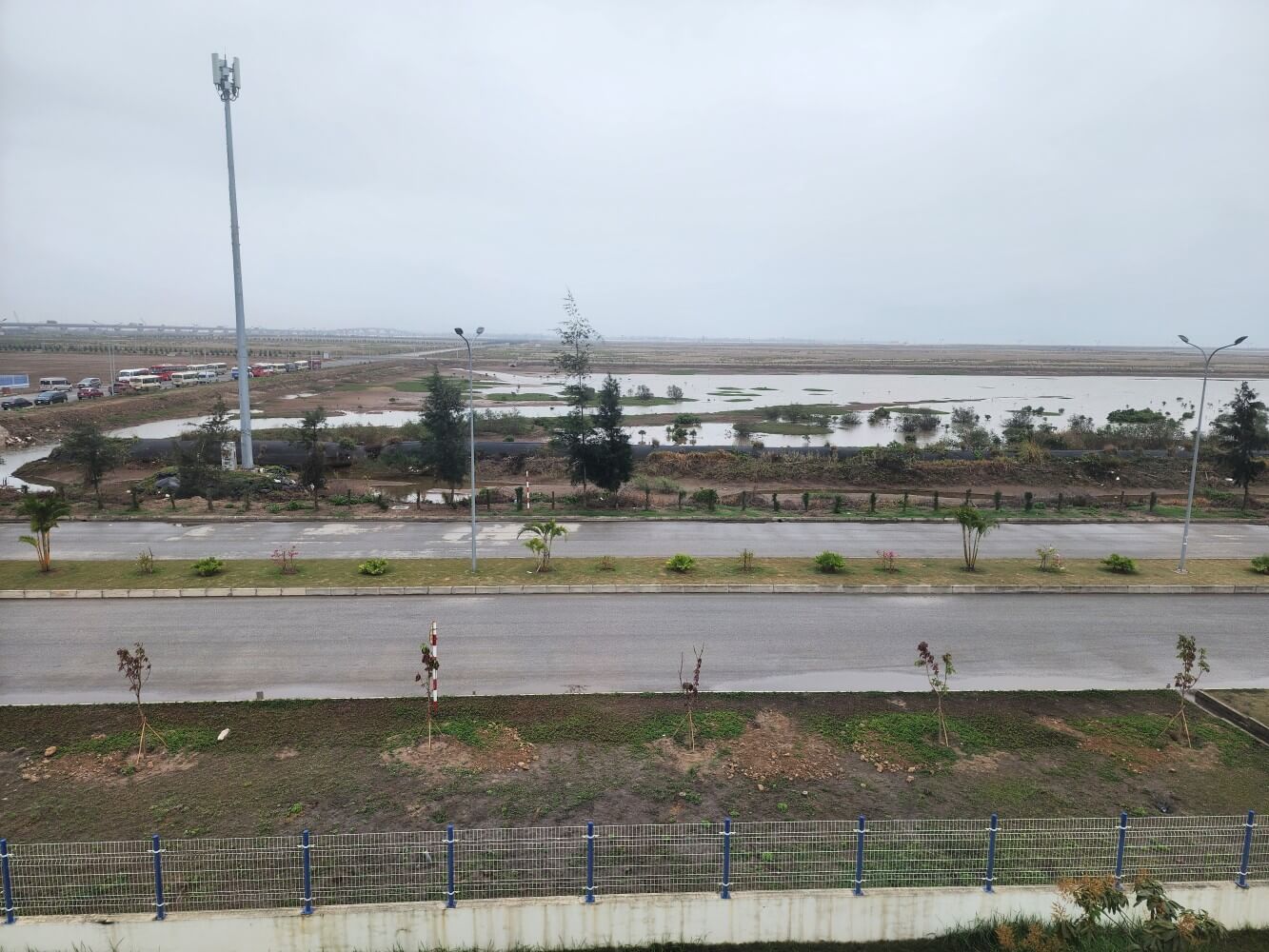
Hải Phòng. The most important port in Vietnam. All the land beyond the road used to be ocean.
Labor
I asked my suppliers what their biggest challenge was, and almost every foreign-owned factory answered with the same response: human resources. And it’s not just because Vietnam only has 100 million people.
Labor in Vietnam costs about 65% of what it does in China — but it’s also about 65% as efficient. I didn’t capture which regions of China were being compared, whether labor cost was burdened, or what efficiency metric was used, but multiple suppliers corroborated these two rough approximations. One constant source of frustration for foreign leadership was the Vietnamese labor’s refusal to work extra shifts. While Chinese workers often live in dormitories attached to their factories and work aggressively long hours, Vietnamese workers clock in, clock out, and go home to their families. I was told it’s actually illegal in Vietnam to have living quarters attached to factories.
But it’s probably inaccurate to attribute this difference only to culture. In China, a lot of factory labor comes from inland provinces with low costs of living, while manufacturing tends to happen in the more expensive, but higher paying, coastal regions. There’s a strong incentive to grind, save, and take the money back to where the purchasing power is greater. In contrast, one major Vietnamese supplier told me that 60% of their workforce grew up in the same town as the factory.
Retention can also be tricky. One foreign-owned factory told me that after hiring and training local workers, it was common for those workers to leave and take jobs at Vietnamese companies. Another supplier said they started paying above China labor rates just to retain talent and incentivize extra shifts.
In contrast to the foreign-owned factories, Vietnamese-owned factories didn’t cite labor as a challenge. Some reported annual turnover between 1%- 5%. That stat aligns with something a new friend shared with me: Vietnamese solidarity is a cultural tenet.
You’re wondering why the disparity. It’s not my place to know, but I can tell you that Vietnam was occupied by China for ~1000 years starting at around the turn of the era [BC to AD]. While “1000 years of war” is a nice little heuristic punchline, and it’s reasonable to try to utilize it to explain my observations, it would be reductivist and intellectually unethical to do so. What you can responsibly do is to reflect on your own country’s historical conflicts and how their impact manifests in your modern-day culture.
One thing worth noting: The foreign-owned factories that empowered Vietnamese leaders, or had Vietnamese leadership already in place, reported far fewer labor challenges.
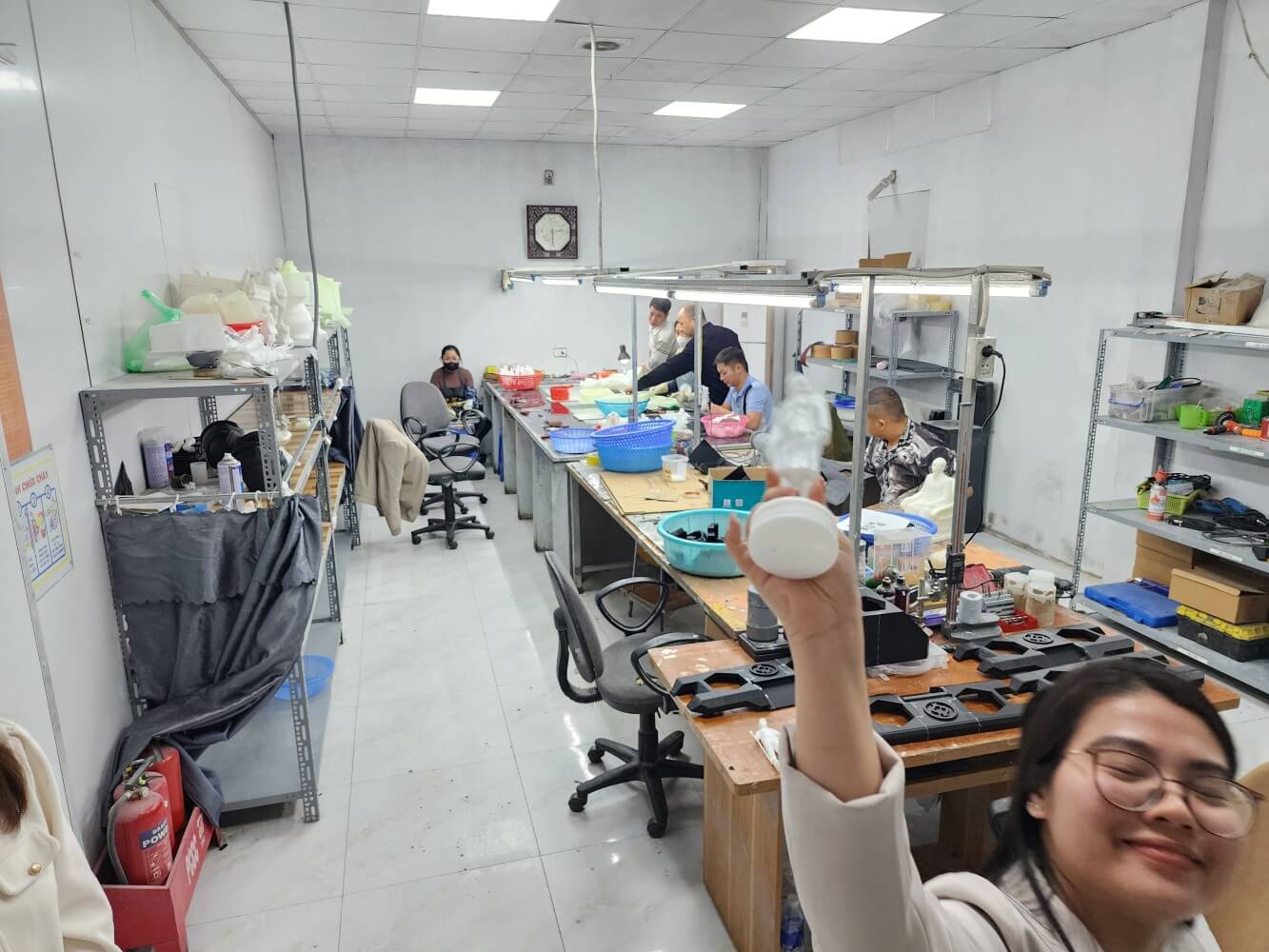
Ngoc and the finishing team showing off!
Is Vietnam the “Next China”?
No, but not because of anything Vietnam is or isn’t doing. It’s because there will never be a “next China.”
Good manufacturing ecosystems are built on infrastructure, technical capability, business-friendly policy, a strong labor pool, and access to both healthy domestic and foreign markets. And let’s not pretend the Chinese “996” isn’t part of that equation (working 9 a.m. to 9 p.m., 6 days a week). Expecting any Southeast Asian country to overcome an incumbent with a 30-year head start and 1.4 billion people is unrealistic — especially when the incumbent is guiding the “exodus.”
The better question is: What should you build in Vietnam?
If you’re making components or parts — yes. The suppliers I visited were on par with anything I’ve seen in China.
If you’re doing FATP for IP reasons — also yes. I believe Vietnamese culture is well suited for protecting IP. But Vietnamese-owned factories may need your support if you’re bringing up lines for complex products, and you may encounter a slower time to market.
If you’re doing FATP purely for landed-in-USA cost reasons — maybe. If the U.S. throws a bad tariff at Vietnam or if the RVC requirement outpaces local supply chain capabilities, you won’t save money by assembling there.
If my observations inform your decision-making, then take this with you too: Never bet against the Vietnamese people.
In multiple factories in China, I encountered signs explicitly stating “Customer is God.” Admittedly, it feels pretty darn good — if not a bit sacrilegious — to be referred to as the almighty. But you should never expect that level of reverence from Vietnamese suppliers. What you should expect is an inalienable sense of self-worth and a baseline expectation of equality.
You won’t be God. But you can become partners.
And coincidentally, the best Chinese supplier relationships I’ve had were also founded under the same principle.
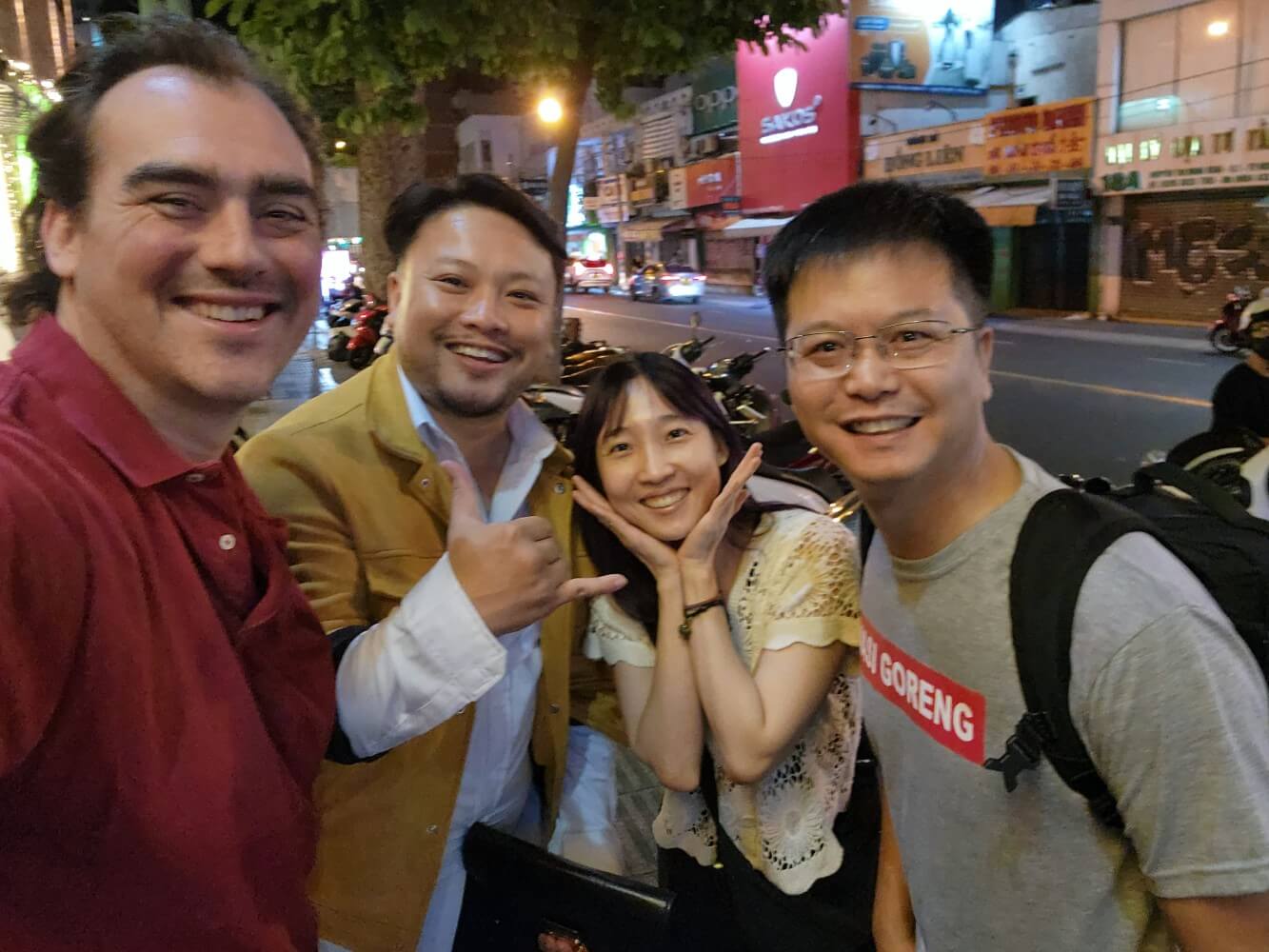
My new buddies Minh, Li Xian, and Ning
Brogan is a doula for early stage hardware startups. During his decade in startups as employee #2, 5, 9, 12, and 40, he has shipped the world’s first handheld 6-lead EKG, shipped the world’s thinnest multi-touch pressure sensor, designed a new carbohydrate texture, built a 100kg electromechanical cooking appliance, spent a year in Asia, and a bunch of wild, cool stuff.
informal is a freelance collective for the most talented independent professionals in hardware and hardtech. Whether you’re looking for a single contractor, a full-time employee, or an entire team of professionals to work on everything from product development to go-to-market, informal has the perfect collection of people for the job.